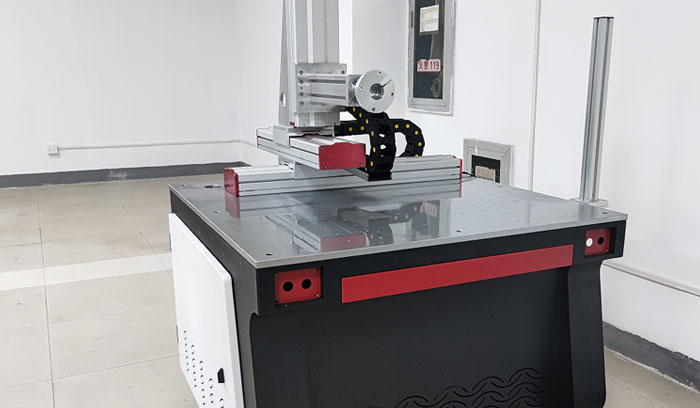
Linear motor is a kind of motor whose motion trajectory can move in a straight direction, which is characterized by smooth motion, high precision, and accurate control of motion position and speed. In many industrial fields, linear motors are widely used, including the automotive industry, machinery manufacturing, medical equipment and other fields. The control mode of linear motor is a very important part, which can affect the running accuracy and efficiency of the machine. The following describes several common linear motor control methods.
1. Voltage control mode
Voltage control mode is the most basic way of linear motor control, mainly by changing the voltage of the motor to control the speed and force of the motor. When the voltage of the motor increases, the speed of the motor also increases, and the force of the motor increases accordingly. Therefore, by adjusting the voltage, the speed and force of the linear motor can be controlled. The voltage control method is simple and easy to control, but in practical applications, because the relationship between voltage and current is very complex, the control accuracy of this method is usually relatively low.
2. Current control mode
Current control mode is one of the more common control modes in linear motor, by controlling the current size of linear motor to control and speed. When the current of the linear motor increases, the force of the motor will also increase, and the speed will also be improved to a certain extent. Compared with voltage control mode, current control mode has better control accuracy. However, it should be noted that the current control mode requires the installation of a current sensor, which also increases the cost of the linear motor.
3. Magnetic field control mode
The magnetic field control method is to control the force and speed of the motor by changing the magnetic field of the motor. Linear motors generate motion through the interaction of current and magnetic field, so sometimes changing the magnetic field can control the motor's motion more directly. Usually, in the linear motor, the magnetic field control mode needs to be equipped with a magnetic field sensor in order to monitor the magnetic field changes of the motor, so as to achieve control.
4. PWM control mode
The PWM (pulse width modulation) control mode is controlled by changing the on-time of the linear motor voltage. Usually, the execution process of the PWM control mode is to convert the voltage of the DC power supply into a pulse surge through high-frequency modulation, and then generate a change in the magnetic field through the current conductor distributed on the linear motor by the motor driver. The PWM control method has high precision and can maintain high efficiency under different loads. However, the PWM control mode needs to be implemented with a sophisticated controller, and the cost is high.
5. Closed-loop control mode
The closed-loop control method is a kind of control method that feeds back the measurement signal to the controller and modifies the output of the controller in real time. Usually, in the closed-loop control mode, the linear motor will be installed with an encoder or Hall sensor to feedback the speed, position and other parameters of the motor, so as to achieve higher precision control. The closed-loop control method has high accuracy, but requires very precise components of the equipment, so the cost is relatively high.
To sum up, different control methods have their own advantages and disadvantages and application occasions, choose the control method suitable for the control requirements to ensure the stable and efficient operation of the linear motor.
No. 3, Guangda Road, Zhitang Industrial Park, Changshu City