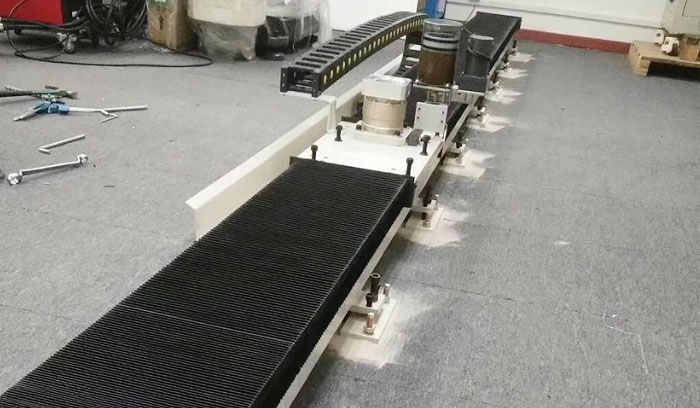
Robots have been widely used in industrial production, medical, military, service robots and other fields. In the construction of robots, the basic movement number can be realized by appropriately increasing the number of motors and mechanical structure design, but there will be certain jitter in the actual movement process, so whether the robot design should consider anti-jitter is a more important issue.
In the working process of the robot, the robot realizes the control and operation of the object or scene through continuous movement. In this process, the movement of the robot is very fine and accurate, but due to the characteristics of its power system, the robot often has a certain jitter when moving, which is caused by the limitation of mechanical transmission. In addition, the influence of the environment is also an important source of jitter, such as wind, earthquake, collision between the robot and other objects, and ground vibration and other factors will have an impact on the movement of the robot.
The seventh axis of the robot is the end effector of the robot, which plays an important role. Therefore, in the design process of the robot, considering that the normal work of the robot needs to ensure good motion quality and accuracy, the seventh axis design of the robot also needs to consider anti-shake.
There are many ways to achieve anti-shake, they can prevent the robot from different angles. The following describes some measures to prevent the seventh axis of the robot from shaking:
1. Use high-speed and stable electric actuators
The stability of the robot mainly comes from its electric actuator, and the high-speed stable electric actuator can prevent the jitter caused by the overload of the motor, and also ensure the accuracy of the robot.
2. Minimize adverse effects
In the design of the robot, as far as possible to reduce adverse effects, such as external force, wear, etc., so as to reduce the impact of the robot, thus producing a good stability effect.
3. Use materials with high stiffness
The use of materials with higher stiffness in the robot can reduce the inclination of the transmission chain or even break, if the inclination of the transmission chain is too large, it will lead to the deterioration of the anti-shake effect of the robot.
4. Control technologyIn robot design, advanced control technology can be used to achieve high-precision motion, such as PID control, smooth control, etc. These control technologies can achieve more stable and accurate motion by reducing vibration, correcting motion errors, and reducing robot motion when it is not needed.
5. Other factors
When the seventh axis is anti-shaking, other factors should be considered, such as the center of gravity of the robot and the spatial position relationship between the robot and the peripheral equipment, etc., and the design rationality in these aspects also directly affects the stability of the robot.
In summary, the anti-shake design of the seventh axis of the robot is very important in the design of the robot, which is related to the accuracy and stability of the robot, and will have an impact on the work efficiency and life of the robot. Therefore, the anti-shake design of the seventh axis should be fully considered in the design of the robot, and effective measures should be taken from multiple angles to ensure that the robot can work smoothly and have higher motion accuracy.
No. 3, Guangda Road, Zhitang Industrial Park, Changshu City